
Six sigma คืออะไร
Six sigma เป็นการบริหารที่มุ่งเน้นในการลดความผิดพลาด ลดความสูญเปล่า และลดการแก้ไขตัวชิ้นงาน และสอนให้พนักงานรู้แนวทางในการทำธุรกิจอย่างมีหลักการ และจะไม่พยายามจัดการกับปัญหาแต่จะพยายามกำจัดปัญหาทิ้ง Six sigma จะดีที่สุดเมื่อทุกคนในองค์การร่วมมือกันตั้งแต่ CEO ไปจนถึงบุคลากรทั่วไปในองค์การ ซึ่ง Six sigma เป็นการรวมกันระหว่างอานุภาพแห่งคน (Power of people) และอานุภาพแห่งกระบวนการ (Process Power) ซึ่งถ้าตัว Six sigma มีค่าสูงหรือมีความผันแปรมากขึ้นเท่าไร ก็เปรียบเสมือนมีการทำข้อผิดพลาดมากขึ้นเท่านั้น ซึ่งโอกาสที่จะเกิดข้อผิดพลาดตัวนี้เรียกว่า DPMO (Defects Per Million Opportunities)
Six sigma จึงถูกนำมาใช้เป็นชื่อเรียกของวิธีการปรับปรุงประสิทธิภาพในขบวนการใด ๆ โดยมุ่งเน้นการลดความไม่แน่นอน หรือ Variation และการปรับปรุงขีดความสามารถในการทำงานให้ได้ตามเป้าหมายที่กำหนด เพื่อนำมาซึ่งความพอใจของลูกค้า และผลที่ได้รับสามารถวัดเป็นจำนวนเงินได้อย่างชัดเจน ไม่ว่าจะเป็นการเพิ่มรายได้ หรือลดรายจ่ายก็ตาม
แนวคิดพื้นฐานของ Six sigma
การพัฒนาองค์การแบบ six sigma เป็นการพัฒนาที่มุ่งเน้นความเป็นเลิศ ซึ่งได้มีการกำหนดแนวทางในด้านต่าง ๆ ได้แก่ ด้านการสื่อสาร การสร้างกลยุทธ์ และนโยบาย การกระจายนโยบาย การจูงใจ และการจัดสรรทรัพยากรในองค์การให้เหมาะสม เพื่อให้การปรับปรุงองค์การเป็นไปอย่างต่อเนื่องและเป็นระบบ โดยเน้นการมีส่วนร่วมของพนักงานที่มีความสามารถ มีความตั้งใจที่จะปรับปรุง ต้องได้รับความรู้ที่เพียงพอต่อการปรับปรุง รวมทั้งมีทีมที่มีความสามารถและมีความตั้งใจที่จะปรับปรุง มีทีมที่ปรึกษาที่มีความเชี่ยวชาญและมีประสบการณ์สูงคอยให้ความช่วยเหลือสนับสนุน เพื่อให้ความผิดพลาดในการผลิตและการบริการมีน้อยที่สุด แนวความคิดการบริหารปรับปรุงองค์การแบบ six sigma มีความแตกต่างจากแนวความคิดในการบริหารแบบเดิม ที่เน้นการปรับปรุงการทำงานโดยเริ่มจากผู้บริหาร แล้วจึงกระจายให้หน่วยงานต่าง ๆ ในองค์การปรับปรุง โดยขาดระบบการให้คำปรึกษาแนะนำและการช่วยเหลือที่เหมาะสม
แนวคิดแบบ six sigma
เน้นให้พนักงานแต่ละคนสร้างผลงานขึ้นมาโดย
1. การตั้งทีมที่ปรึกษา (Counselling groups) เพื่อให้คำแนะนำพนักงานในการกำหนดแผนปรับปรุงการทำงาน
1. การตั้งทีมที่ปรึกษา (Counselling groups) เพื่อให้คำแนะนำพนักงานในการกำหนดแผนปรับปรุงการทำงาน
2. การให้ทรัพยากรที่จำเป็นต่อการปรับปรุง (Providing resource)
3. การสนับสนุนแนวความคิดใหม่ ๆ (Encouraging Ideas) เพื่อให้โอกาสพนักงานในการเสนอแนะความคิดเห็นใหม่ๆ
4. การเน้นให้พนักงานสามารถคิดได้ด้วยตัวเอง (Thinking) เพื่อให้พนักงานสามารถกำหนดหัวข้อการปรับปรุงขึ้นเอง ภายใต้ข้อกำหนดของผู้บริหารองค์การ
แนวคิดการบริหารองค์การแบบเดิม
1.ใช้การแก้ปัญหาแบบวันต่อวัน ทักษะในการเรียนรู้ของพนักงานจะเน้นที่การเรียนรู้จาการทำงานจริงเป็นหลัก โดยมีความเชื่อว่าถ้ามีคนเข้าไปดูปัญหาอย่างจริงจังจะสามารถแก้ปัญหาได้ ซึ่งบางครั้งการแก้ปัญหาไม่ได้มาจากการแก้ไขที่สาเหตุแต่ก็สามารถแก้ไขปัญหาได้
2.ผลของการแก้ไขปัญหาจะต้องหายขาด
3.คัดเลือกพนักงานที่ทำงานประจำมาทำการแก้ไขปัญหา โดยแก้ไขเฉพาะหน่วยงานของตนเอง ถ้าปัญหาเกิดจากหน่วยงานอื่นก็จะขอร้องให้หน่วยงานนั้น ๆ ทำการแก้ไข
4.ผู้นำคือผู้ที่สามารถแก้ไขปัญหาในปัจจุบันได้
5.ใช้ประสบการณ์และความชำนาญเป็นหลักในการปรับปรุง เพราะเห็นผลสำเร็จได้ง่าย
6.ความรับผิดชอบเป็นหน้าที่ของพนักงานแต่ละคนต้องปฏิบัติ
2.ผลของการแก้ไขปัญหาจะต้องหายขาด
3.คัดเลือกพนักงานที่ทำงานประจำมาทำการแก้ไขปัญหา โดยแก้ไขเฉพาะหน่วยงานของตนเอง ถ้าปัญหาเกิดจากหน่วยงานอื่นก็จะขอร้องให้หน่วยงานนั้น ๆ ทำการแก้ไข
4.ผู้นำคือผู้ที่สามารถแก้ไขปัญหาในปัจจุบันได้
5.ใช้ประสบการณ์และความชำนาญเป็นหลักในการปรับปรุง เพราะเห็นผลสำเร็จได้ง่าย
6.ความรับผิดชอบเป็นหน้าที่ของพนักงานแต่ละคนต้องปฏิบัติ
แนวคิดการบริหารแบบ six sigma
1.เน้นสร้างทักษะและการเรียนรู้ให้แก่พนักงานอย่างเป็นระบบ และเข้มงวด รู้ปัญหาและกำหนดเป็นโครงการปรับปรุงทั้งระยะสั้นและระยะยาว
2.วัดที่ผลการปรับปรุงเป็นหลัก
3.ใช้ทีมงานที่มีผลประเมินการทำงานดี หรือ ดีเยี่ยม มาทำการปรับปรุงและตัดสินใจให้คนเก่งมีเวลาถึง 100 % เพื่อแก้ปัญหาให้กับองค์การ
4.สร้างผู้นำโครงการให้เกิดขึ้นในอนาคต
5.ใช้ข้อมูลเป็นตัวตัดสินใจเท่านั้น
6.เน้นความรับผิดชอบในการทำโครงการ
7.การให้คำมั่นสัญญามาจากผู้บริหาร
2.วัดที่ผลการปรับปรุงเป็นหลัก
3.ใช้ทีมงานที่มีผลประเมินการทำงานดี หรือ ดีเยี่ยม มาทำการปรับปรุงและตัดสินใจให้คนเก่งมีเวลาถึง 100 % เพื่อแก้ปัญหาให้กับองค์การ
4.สร้างผู้นำโครงการให้เกิดขึ้นในอนาคต
5.ใช้ข้อมูลเป็นตัวตัดสินใจเท่านั้น
6.เน้นความรับผิดชอบในการทำโครงการ
7.การให้คำมั่นสัญญามาจากผู้บริหาร
หลักการสำคัญของกลยุทธ์ Six sigma
การบรรลุกลยุทธ์ที่สำคัญของ six sigma ซึ่งเกี่ยวข้องกับขั้นตอน 5 ขั้นตอน ซึ่งประกอบด้วย Define - Measure – Analyze – Improve – Control

1. Define คือ ขั้นตอนการระบุและคัดเลือกหัวข้อเพื่อการดำเนินการตามโครงการ
Six Sigma ในองค์กร โดยมีขั้นตอนการคัดเลือกโครงการ ดังนี้
Six Sigma ในองค์กร โดยมีขั้นตอนการคัดเลือกโครงการ ดังนี้
- ขั้นตอนที่ 1 โครงการนั้นต้องสอดคล้องกับเป้าหมายหลักขององค์กร (Business Goal)
- ขั้นตอนที่ 2 มอบหมายให้ฝ่ายต่างๆ ที่เสนอโครงการไปพิจารณาหากลยุทธ์ (Strategy) ในการดำเนินงานที่สอดคล้องกับเป้าหมายหลักขององค์กร (ตามขั้นตอนที่ 1)
- ขั้นตอนที่ 3 แต่ละฝ่ายนำเสนอกลยุทธ์ในการดำเนินการให้ผู้บริหารทราบ และเมื่อผู้บริหารเห็นชอบแล้ว ให้กลับไปกำหนดพื้นที่ที่จะดำเนินงาน (High Potential Area)
- ขั้นตอนที่ 4 ซึ่งเป็นขั้นตอนสุดท้าย หลังจากกำหนดพื้นที่ที่จะดำเนินการได้แล้ว ให้แต่ละฝ่ายกลับไปพิจารณาหัวข้อย่อยที่จะใช้ในการดำเนินการ
2. Measure เป็นขั้นตอนการวัดความสามารถของกระบวนการที่เป็นจริงในปัจจุบัน ขั้นตอนการวัดจะแบ่งการดำเนินงานออกเป็น 5 ขั้นตอน คือ
- ขั้นตอน Plan Project with Metric คือ การวางแผนและดำเนินการคัดเลือกตัวชี้วัดที่เหมาะสมในการดำเนินการโครงการ
- ขั้นตอน Baseline Project คือการวัดค่าความสามารถของกระบวนการที่เป็นจริงในปัจจุบัน โดยวัดผ่านตัวชี้วัดต่างๆ ที่เลือกสรรมาจากขั้นตอน Plan Project with Metric
- ขั้นตอน Consider Lean Tools คือ วิธีการปรับปรุงกระบวนการด้วยการใช้เทคนิคต่างๆ ของวิศวกรรมอุตสาหการ
- ขั้นตอน Measurement System Analysis (MSA) ขั้นตอนนี้เป็นขั้นตอนที่สำคัญมากเป็นขั้นตอนการตรวจสอบเครื่องมือหรืออุปกรณ์ในการทำงานว่ามีความปกติหรือไม่ก่อนจะลงมือปฏิบัติงาน
- ขั้นตอน Organization Experience หมายถึง ขั้นการนำประสบการณ์ที่ผ่านมาขององค์กร จะช่วยคิดในการแก้ไขปัญหา
3. Analyze ขั้นตอนนี้คือการวิเคราะห์สาเหตุของปัญหาหลัก ซึ่งเป็นการวิเคราะห์ในเชิงสถิติเพื่อระบุสาเหตุหลักที่ส่งผลโดยตรงต่อปัญหานั้น ซึ่งเรียกสาเหตุหลักนี้ว่า KPIV (Key Process Input Variable) ซึ่งต้องสามารถระบุให้ชัดเจนว่า อะไรคือ KPIV ของปัญหาและต้องสามารถเชื่อมโยงกับ ตัวหลักของกระบวนการ หรือที่เรียกว่า KPOV (Key Process Output Variable) ให้ได้ หลักการสถิติที่ใช้ในการวิเคราะห์ ได้แก่ การตรวจสอบสมมติฐาน (Hypothesis Testing) ผังการกระจาย (Scattering Diagram) การวิเคราะห์การถดถอย (Regression Analysis) เป็นต้น
4. Improvement ขั้นตอนนี้คือการปรับตั้งค่าสาเหตุหลัก (KPIV) โดยมีจุดประสงค์เพื่อให้ผลลัพธ์ของกระบวนการเป็นไปตามต้องการ ด้วยการใช้เทคนิคการออกแบบทดลอง(Design of Experiment : DOE) เพื่อปรับตั้งค่าสภาวะต่างๆของกระบวนการให้เป็นไปตามความต้องการ
5. Control ขั้นตอนนี้เป็นขั้นตอนสุดท้าย ซึ่งต้องดำเนินการออกแบบระบบควบคุณคุณภาพของกระบวนการเพื่อให้เกิดความมั่นใจว่ากระบวนการจะย้อนไปมีปัญหาเหมือนเดิมอีก DMAIC เป็นวิธีการพื้นฐานในกระบวนการ อาจให้คำจำกัดความสั้นๆ ได้ว่า Define: ต้องไม่มีการยอมรับความผิดพลาด Measure : กระบวนการภายนอกที่หาจุดวิกฤตเชิงคุณภาพ Analysis : ทำไมความผิดพลาดจึงเกิดขึ้น Improve : การลดความผิดพลาดที่เกิดขึ้น Control : ต้องควบคุมให้เป็นไปตามเป้าหมาย
องค์ประกอบสำคัญที่มีบทบาทต่อ six sigma
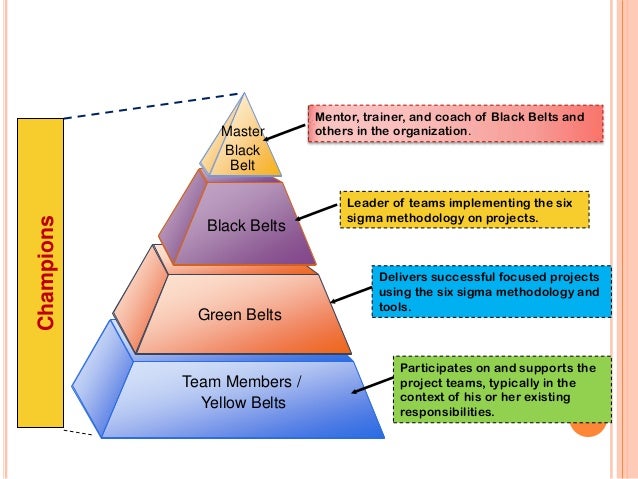
โครงสร้างและหน้าที่รับผิดชอบ ของ Six sigma ประกอบด้วย
1.Champion เป็นชื่อเรียกผู้ที่มีความรับผิดชอบสูงสุดต่อผลสำเร็จในงาน หรือผู้บริหารระดับสูง (Executive-Level Management) สนับสนุนให้เป้ามายของงานสำคัญประสบความสำเร็จ รณรงค์และผลักดันให้เกิดองค์การ six sigma และเกิดกระบวนการปรับปรุงองค์การอย่างต่อเนื่อง ขจัดอุปสรรค ให้รางวัลหรือค่าตอบแทน ตอบปัญหา อนุมัติโครงการ กำหนดวิสัยทัศน์โครงการ สนับสนุนทรัพยากรในด้านบุคลากร งบประมาณ เวลา สถานที่ กำลังใจ และความชัดเจนในหน้าที่ ผลักดันให้มีจำนวน Black Belt และ Green Belt ที่เหมาะสมในองค์การ มีหน้าที่ติดตามความก้าวหน้าของโครงการปรับปรุง ให้สอดคล้องกับเป้าหมายขององค์การ ส่งเสริมและสนับสนุนการสร้างวัฒนธรรมในการปรับปรุงให้เกิดขึ้นในองค์การ โดยอาศัยการสื่อสาร การตั้งคำถามเพื่อย้ำให้เกิดแนวความคิดแบบ six sigma มีการชมเชยและการให้ประกาศนียบัตรแก่พนักงานในองค์การ มีการคัดเลือกโครงการปรับปรุงที่ดีเยี่ยมและการให้รางวัลเมื่อพนักงานปฏิบัติงานมีประสิทธิภาพ
2. Six sigma Director มีหน้าที่นำและบริหารองค์การให้สำเร็จบรรลุแนวทาง six sigma ภายในหน่วยงานทางธุรกิจตนเอง เป็นผู้กำหนดแนวทางในการปฏิบัติและนโยบายการดำเนินงานของ six sigma สนับสนุนกิจกรรมต่าง ๆ ที่สำคัญในการกระจายนโยบายให้เป็นไปอย่างต่อเนื่อง
3. Master Black Belt คือ ผู้ชำนาญการด้านเทคนิค และเครื่องมือสถิติ เป็นผู้มีความรู้และความเชี่ยวชาญในการทำงานเป็นอย่างดี และสามารถถ่ายทอดและให้การอบรมเพื่อสร้างทีม Black Belt และ Green Belt ตลอดการปรับปรุงได้ เป็นผู้ช่วยเลือกโครงการปรับปรุงให้แก่ Champion และเป็นผู้มีความคิดสร้างสรรค์ในการคัดเลือกโครงการปรับปรุง โดยมองในภาพรวมใหญ่ขององค์การ ได้แก่ การปรับปรุงโครงสร้างพื้นฐาน และการเสนอโครงการปรับปรุงที่เชื่อมโยงกันระหว่างหน่วยงานต่าง เป็นต้น
4. Black belt คือ ผู้บริหารโครงการ (Project Manager) และผู้ประสานงาน (Facilitator )ได้รับการรับรองว่าเป็นสายดำชั้นครู Black belt เป็นการบ่งบอกถึงระดับความสามารถสูงสุดของนักกีฬายูโด จะทำหน้าที่เป็นหัวหน้าโครงการ บริหารลูกทีมที่มีลักษณะข้ามสายงาน ซึ่งในการบริหาร six sigma จะประกอบไปด้วยการทำโครงการย่อยที่คัดเลือกจากปัญหาที่มีอยู่ในกระบวนการต่าง ๆ ขององค์การ กระจายกลยุทธ์และนโยบายของบริษัทไปยังระดับปฏิบัติการ ผลักดันความคิดของ Champion ให้เกิดขึ้นและให้ความช่วยเหลือ Master Black Belt six sigma Director และ Champion นอกจากนี้ยังเป็นผู้ค้นหาปัญหาและอุปสรรคที่อยู่ในองค์การ และวิเคราะห์หาปัจจัยที่มีความจำเป็นในการทำให้องค์การบรรลุความพึงพอใจของลูกค้า เป็นผู้บริหารโครงการในแต่ละขั้นตอนตามแนวทาง six sigma ประกอบด้วย กระบวนการวัด การวิเคราะห์ การปรับปรุง และการควบคุม โดยให้เกิดการกระจายผลการปรับปรุงไปสู่การปฏิบัติ รายงานความก้าวหน้าของโครงการให้ผู้บริหารระดับสูงทราบ Black Belt จะต้องทำหน้าที่ในการโน้มน้าวทีมงานได้อย่างมีประสิทธิภาพ คัดเลือกเครื่องมือที่จะนำมาใช้ในการปรับปรุงได้อย่างเหมาะสม เก็บรวบรวมปัจจัยที่เกี่ยวข้องกับโครงการปรับปรุงจากแหล่งข้อมูลต่าง ๆ ภายในองค์การ ทั้งจากพนักงานจนถึงระดับผู้จัดการ สร้างความมั่นใจว่าผลลัพธ์ที่ได้จากการปรับปรุงสามารถคงอยู่ได้ตลอดไป
Black Belt ต้องได้รับการฝึกอบรมเพื่อให้มีความรู้ทีสำคัญในการปรับปรุงการทำงาน ซึ่งความรู้หลัก ๆ ของ Black Belt เพื่อการทำโครงการปรับปรุงที่จะได้รับประกอบด้วย
4.1 ความรู้ทางสถิติ
4.2 ความรู้ทางด้านการบริหารโครงการ
4.3 ความรู้ทางด้านการสื่อสารและการเป็นผู้นำโครงการ
4.4 ความรู้เพื่อการปรับปรุงคุณภาพอื่น ๆ
4.1 ความรู้ทางสถิติ
4.2 ความรู้ทางด้านการบริหารโครงการ
4.3 ความรู้ทางด้านการสื่อสารและการเป็นผู้นำโครงการ
4.4 ความรู้เพื่อการปรับปรุงคุณภาพอื่น ๆ
5. Green belt คือพนักงานที่ทำหน้าที่โครงการ เป็นผู้ที่รับการรับรองว่ามีความสามารถเทียบเท่านักกีฬายูโดในระดับสายเขียว ซึ่งในการบริหาร six sigma นั้น ผู้ที่ทำหน้าที่เป็น Green belt จะเป็นผู้ช่วยของ Black belt ในการทำงาน ทำหน้าที่ในการปรับปรุงโดยใช้เวลาส่วนหนึ่งของการทำงานปกติ นำวิธีการปรับปรุงตามแนวทาง six sigma ไปใช้ในโครงการได้ สามารถนำเอาแนวความคิดและวิธีการปรับปรุงไปขยายผลต่อในหน่วยงานของตนเองได้
6. Team Member ในโครงการทุกโครงการจะต้องมีสมาชิกทำงาน 4-6 คน โดยเป็นตัวแทนของคนที่ทำงานในกระบวนการที่อยู่ในขอบข่ายของโครงการ
ส่วนสำคัญที่สุดในการทำ Six sigma คือ โปรเจ็ก แชมเปี้ยน ซึ่งจะมีหน้าที่ในการดูแลให้การสนับสนุน และจัดหางบประมาณที่เพียงพอให้แต่ละ Six sigma และยังคอยสนับสนุน แบล็กเบลต์
ส่วนสำคัญที่สุดในการทำ Six sigma คือ โปรเจ็ก แชมเปี้ยน ซึ่งจะมีหน้าที่ในการดูแลให้การสนับสนุน และจัดหางบประมาณที่เพียงพอให้แต่ละ Six sigma และยังคอยสนับสนุน แบล็กเบลต์
ประโยชน์ในการนำ Six Sigma มาใช้ในองค์การ
1. สามารถแก้ปัญหาได้อย่างมีประสิทธิภาพ สร้างกลยุทธ์ใหม่ให้ธุรกิจ
2. สามารถลดความสูญเสียโอกาสอย่างมีระบบและรวดเร็วโดยการนำกระบวนการทางสถิติมาใช้
3. พัฒนาบุคลากรในองค์การให้มีศักยภาพสูงขึ้นตอบสนองต่อกลยุทธ์ได้อย่างรวดเร็ว และปรับองค์การให้เป็นองค์การแห่งการเรียนรู้ (Learning Organization)
4. ช่วยหารระดับคุณภาพของอุตสาหกรรม โดยสามารถเทียบข้ากลุ่มอุตสาหกรรมได้ (Benchmarking)
2. สามารถลดความสูญเสียโอกาสอย่างมีระบบและรวดเร็วโดยการนำกระบวนการทางสถิติมาใช้
3. พัฒนาบุคลากรในองค์การให้มีศักยภาพสูงขึ้นตอบสนองต่อกลยุทธ์ได้อย่างรวดเร็ว และปรับองค์การให้เป็นองค์การแห่งการเรียนรู้ (Learning Organization)
4. ช่วยหารระดับคุณภาพของอุตสาหกรรม โดยสามารถเทียบข้ากลุ่มอุตสาหกรรมได้ (Benchmarking)